MULTIForm
Multiphase Fluid Flow In Nuclear systems
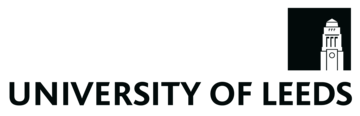
PI: Alastair Baker
MULTIForm (Multiphase Fluid Flow In Nuclear systems) will be part of the NNUF based at the University of Leeds and scheduled to open in October 2023 with the dedicated aim to enable world class research on multiphase fluid flow, at a scale that is representative of a real system. By establishing a state-of-the-art, university-based facility, we will support academic and industrial researchers to understand the many challenging flow systems relevant to current and future research challenges and answer questions on themes of critical importance to the UK nuclear sector; such as precipitation, deposition, erosion and breakup of sludge wastes or CRUD particles, for safe pipeline transportation and reactor operation.
News in here
Our vision for the facility
MULTIForm will enable researchers to understand the turbulence, heat transfer characteristics and the impact of gas injection on liquid mobility in bubbly reactor flows, and critically, future salt reactors. Our facility will provide top-of-the-range instrumentation for high-fidelity validation of computational fluid dynamics models in order to predict performances in a variety of nuclear reactors, transportation or separation units.
Research areas that MULTIForm will support include:
Decommissioning of legacy facilities in the UK
-
Waste retrievals – sludge management in legacy ponds and silos, exploring sludge transport in pipelines and modification of its behaviour to enable improved flow, mixing and separation of wastes during processing activities.
-
Utilisation of the test beds – advanced characterisation instrumentation for online monitoring of nuclear wastes.
-
Effluent treatment wastes – flows through concentrated sediments, transportation and stability of precipitated flocs, and bubble-particle dynamics for effluent separation.
- Highly active liquors – transportation of precipitated fission wastes from storage and evaporation operations, as part of Post Operational Clean Out (POCO) activities.
Advanced reactors
-
Developing main cooling circuits and testing heat transfer in a dynamic salt system for SMR and AMRs.
-
Scaling techniques and processes up from the lab and into industry.
Current reactors and new build
-
Management of ‘crud’ in cooling circuits to examine the rate and mechanisms of particle (corrosion product) deposition on solid surfaces and its impact on clogging cooling circuits.
-
Performance of heat transfer under fouling to examine the rate and mechanisms of particle deposition on solid surfaces and its impact on thermohydraulic performance.
-
Characterisation of bubbly and boiling flows to evaluate flow characteristics, the critical heat flux and departures from nucleate boiling.
Advanced fuel cycles
- Providing direct support to the MSAG, recently convened by BEIS for the development and exploitation of molten salt technologies in the UK. Includes online monitoring/analysis, salt clean-up, materials and fuel cycle integration; where research on dynamic (rather than static) salt systems allows development of novel technology.
MULTIForm consists of 3 major components:
1. A bank of high precision, state-of-the-art, instruments for measuring a wide range of fluid flow properties.
2. A pilot scale test bed, based on a water flow system [pressure (=<5atm), temperature (=<100oC)].
3. A pilot scale test bed, based on a molten chloride flow system [pressure (=<5atm), temperature (=<600oC)].
Both test beds will be reconfigurable to incorporate new specialist instrumentation for fluid flow measurements and/or used to develop new instruments and equipment for future research.
The water test bed
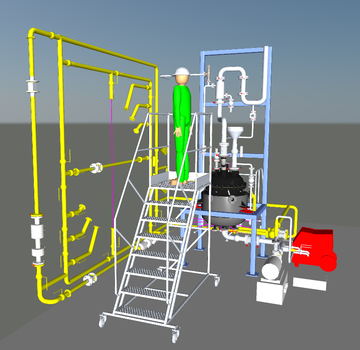
© University of Leeds
The test bed will be constructed in a rigid steel frame with permanent working platforms to allow test sections to be replaced at height and accessed at all five angles, from horizontal to vertical. Thus, the effects of gravity and gravity-driven differences on dispersed phase concentrations can be investigated, which is especially important for buoyancy driven dynamics.
An inline heater prior to the manifold of the different angled pipe loops will bring the temperature of the circulating water up to near boiling point for experiments involving vapour/liquid systems and further heating within the test section will create boiling in-situ. A gas injection point will allow for the generation of bubbly flows (two phase or three phase with solids) at lower temperatures.
The test bed will be able to handle up to 1 M of strong acid and capable of working with solutions of dissolved salts such as nitrates, carbonates, chlorides and borates; to match the chemistry of the systems it is designed to represent.
In addition, the design will allow solids to be introduced throughout the rig at various concentrations, typically in three size ranges:
- Small (1-5 μm) which relate to recycle applications, as well as highly active effluent precipitates and the approximate size of corroded reactor ‘crud’ particles.
- Medium (10-100 μm) which relate to legacy storage applications, for example, transfer of corroded fuel cladding sludge.
- Large (up to 500 μm) which relate to effluent applications, from the transfer of large solid ion exchange and filtration media.
The molten salt test bed
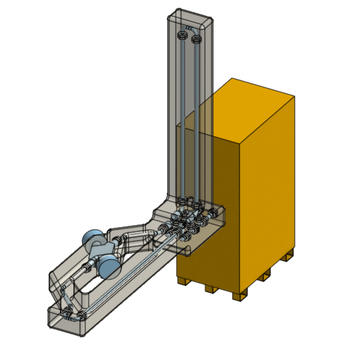
© University of Leeds
The molten salt test bed will use the common halide salt LiCl/KCl chloride eutectic, which acts as an accurate representative for the majority of halide salts systems favoured by the nuclear industry (systems typically functioning in ranges between 450-700oC). The design of the loop will allow gas-liquid systems to be investigated from controlled gas injection in a non-pressurised system.
High-precision instrumentation and testing capabilities
All the measurement techniques mountable within 2m test sections on the two MULTIForm test beds are recognised as the most advanced available for these types of flows and our research team are world experts in applying them.
Our current list of high precision specialist instrumentation and applications includes:
Fluid Properties
Property |
Technique |
Water |
Salt |
---|---|---|---|
Velocity profiling | Constant Temperature Anemometer (CTA) | Yes | |
Multiphase velocity profiling (includes solids) | Ultrasonic Velocity Profiler (UVP) | Yes | Yes |
High Temp UVP Probes | Yes | ||
Particle imaging velocimetry (PIV) | Yes | ||
2D Laser Doppler Velocimetry (LDV) | Yes | Yes |
Solids/gas properties
Property |
Technique |
Water |
Salt |
---|---|---|---|
Size, coalescence and breakage, determining the size and shape of the particles or bubbles | Focussed Beam Reflectometry (FBRM) | Yes | |
Sedimentation/creaming, understand particle phase stability | X-ray dispersion separation analyser | Yes | |
Particle/bubble tracking | High speed imaging camera | Yes | Yes |
Fluid/slurry viscosity | Rheometer | Yes | Yes |
In addition to the above, each test bed will have a range of standard testing instrumentation. These will be high precision equivalents of those found on process plant and other research rigs:
Property |
Technique |
Conditions |
Precision |
---|---|---|---|
Temperature
Water Molten Halide |
Thermocouple on outer surface at multiple points along pipe runs
J-type: PTFE-Cu J-type: Ceramic fibre - NiCR |
-75 to 350°C 0 to 1000°C |
+/- 0.5°C +/- 2.5°C |
Bulk flowrate Mass - gas Mass - water Volume - molten halide |
Flow meters placed at key points Flow meter Flow meter Flow meter |
0.4 to 20 l/min; -10 to 70°C 0.5 to 30 l/min; 5 to 90°C -29 to 500°C |
+/- 0.5% +/- 1.5% +/- 3% |
Pressure Water Molten halide |
Sensors placed at key points Sensors placed at key points |
0 to 15 PSI 0 to 2500 PSI |
+/- 0.25% +/- 0.25% |
Experimental support and expertise
As an NNUF facility, MULTIForm will be open to users from industry, universities in the UK, overseas, and to those eligible to bid for UKRI funds. MULTIForm will have a resident team of research staff, including academic experts in the field and a dedicated experimental officer (Alastair Baker), available to assist with planning, conducting and managing experiments.
What training and educational opportunities can MULTIForm offer for students?
The School of Chemical and Process Engineering at the University of Leeds is home to one of the largest Chemical Engineering UG and PGT programmes in the UK, with up to 200 students per year at Master’s level, who all have individual research projects. Alongside our own UG and PG students, we expect to welcome a substantial number of researchers and researchers-in-training from industry and institutions worldwide. If fluid dynamics or multiphase flows are your areas of interest, we look forward to hearing from you.
Contact
To learn more about what we can offer and how MULTIForm could support your research, please contact Alastair Baker A.R.Baker@leeds.ac.uk
Availability
The design and build of the facility began in February 2022 with the aim to have the facility ready for research teams in the later months of 2023.
© University of Leeds.